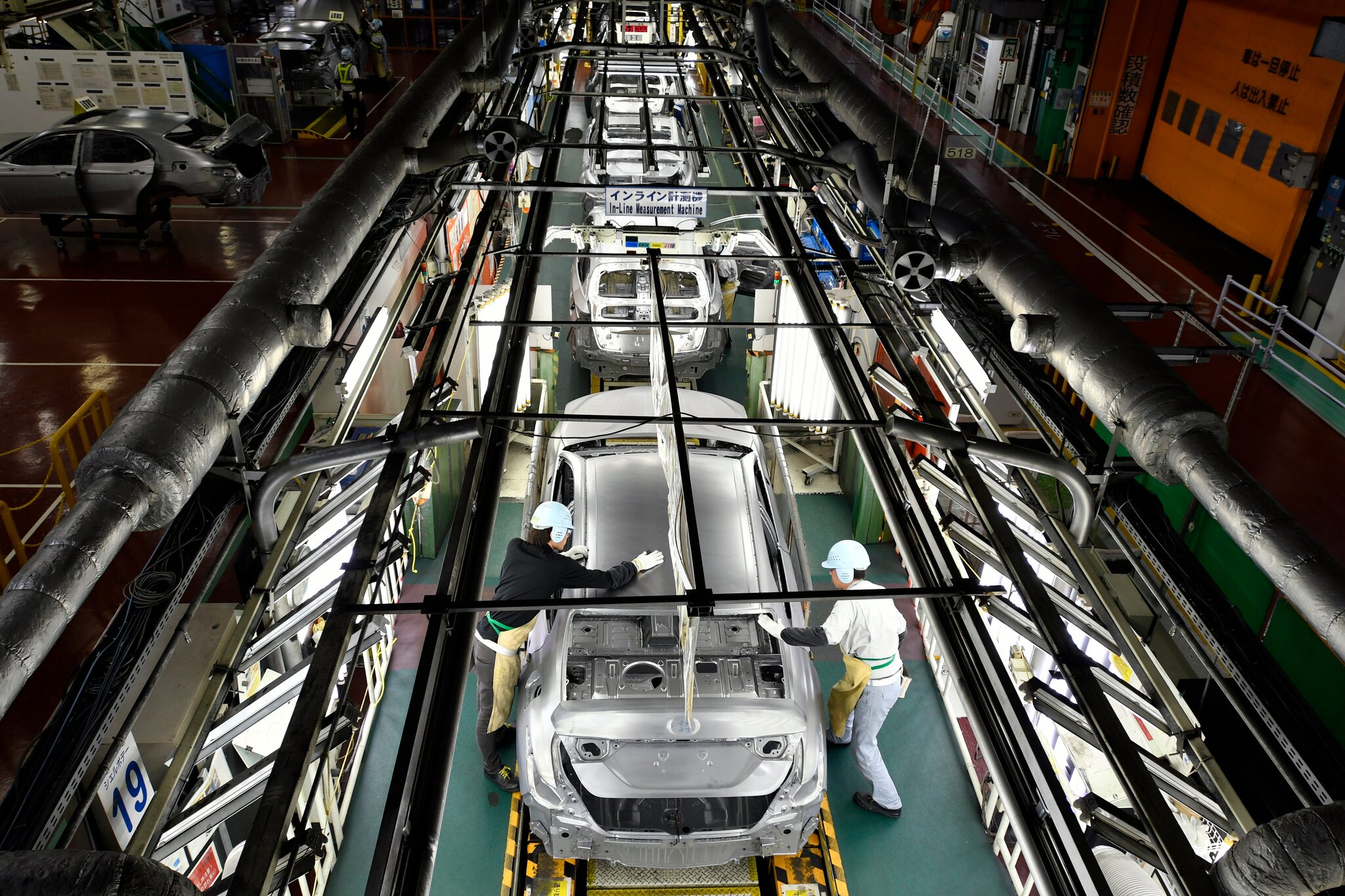
In a surprising turn of events, one of the world’s leading car manufacturers, Toyota, recently found itself in a state of crisis. This crisis wasn’t about car designs or production logistics but rather about something that might sound mundane: insufficient disk space. In this blog post, we’ll reveal why Toyota’ had to shut down 14 of its factories’s Factory shutdown happened in Japan due to computer issues.
We will also discuss the learnings of this infamous catastrophe. Let’s dig in!
The Storage Crisis: Toyota’s Factory Shutdown
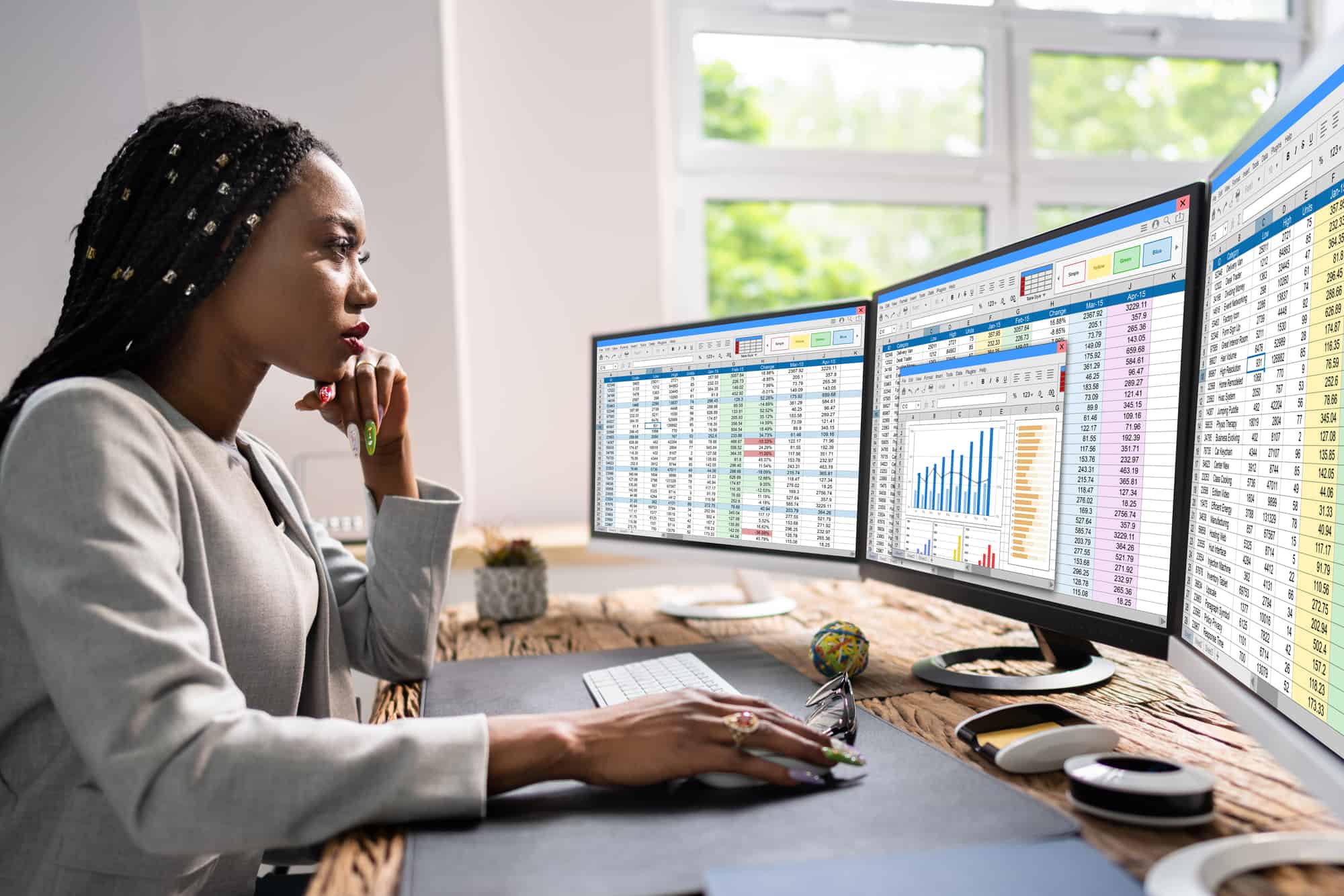
There’s no such thing as excessive storage space, even for leading automobile companies like Toyota!
In late August, Toyota was forced to halt production on 28 assembly lines spread across 14 auto plants in Japan due to computer-related problems. Reuters estimates that these Japan-based plants are responsible for approximately one-third of Toyota’s worldwide car production.
On September 6th, Toyota released additional information on the shutdown, revealing that “the issue was caused by an error resulting from insufficient disk space.”
The Cause of Disruption: System Maintenance Gone Wrong
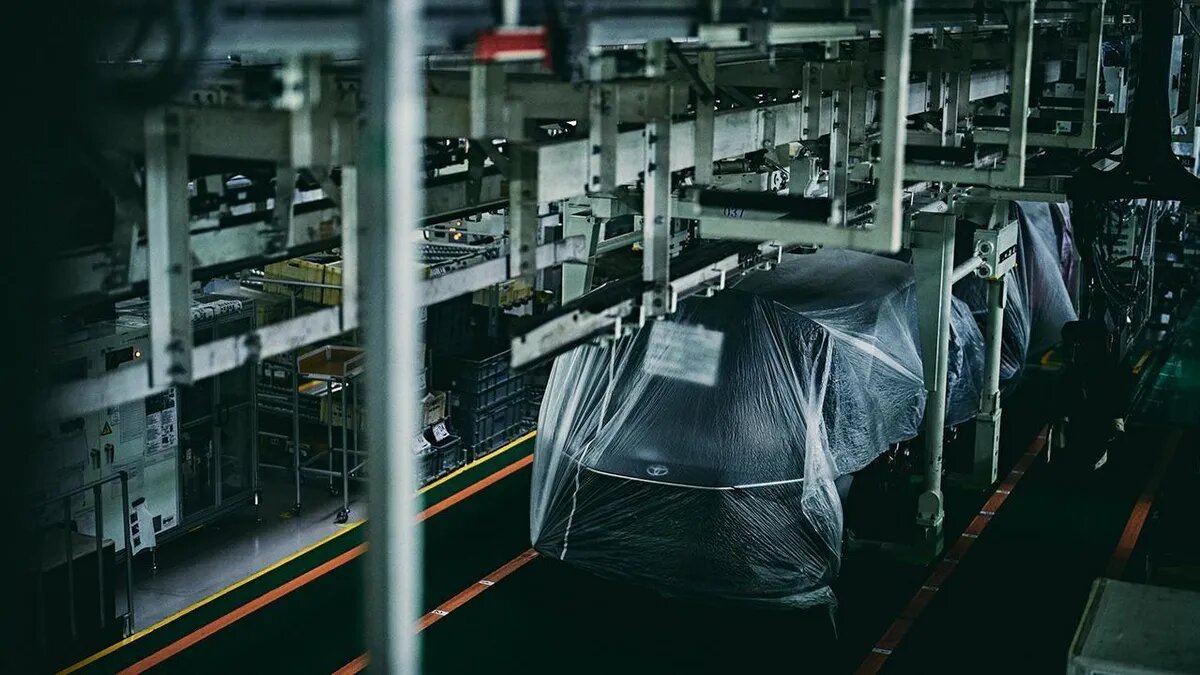
In a statement by Toyota, the recent plant shutdowns were attributed to a system maintenance operation conducted a few days earlier. This maintenance involved the deletion and organization of accumulated data within the database.
Unfortunately, a problem occurred during this process due to insufficient disk space, resulting in a system failure. Additionally, the servers responsible for running the system were also connected to the backup system, which meant that the same issue affected the backup. This situation made it impossible for the company to switch to an alternative system.
Impact on Production
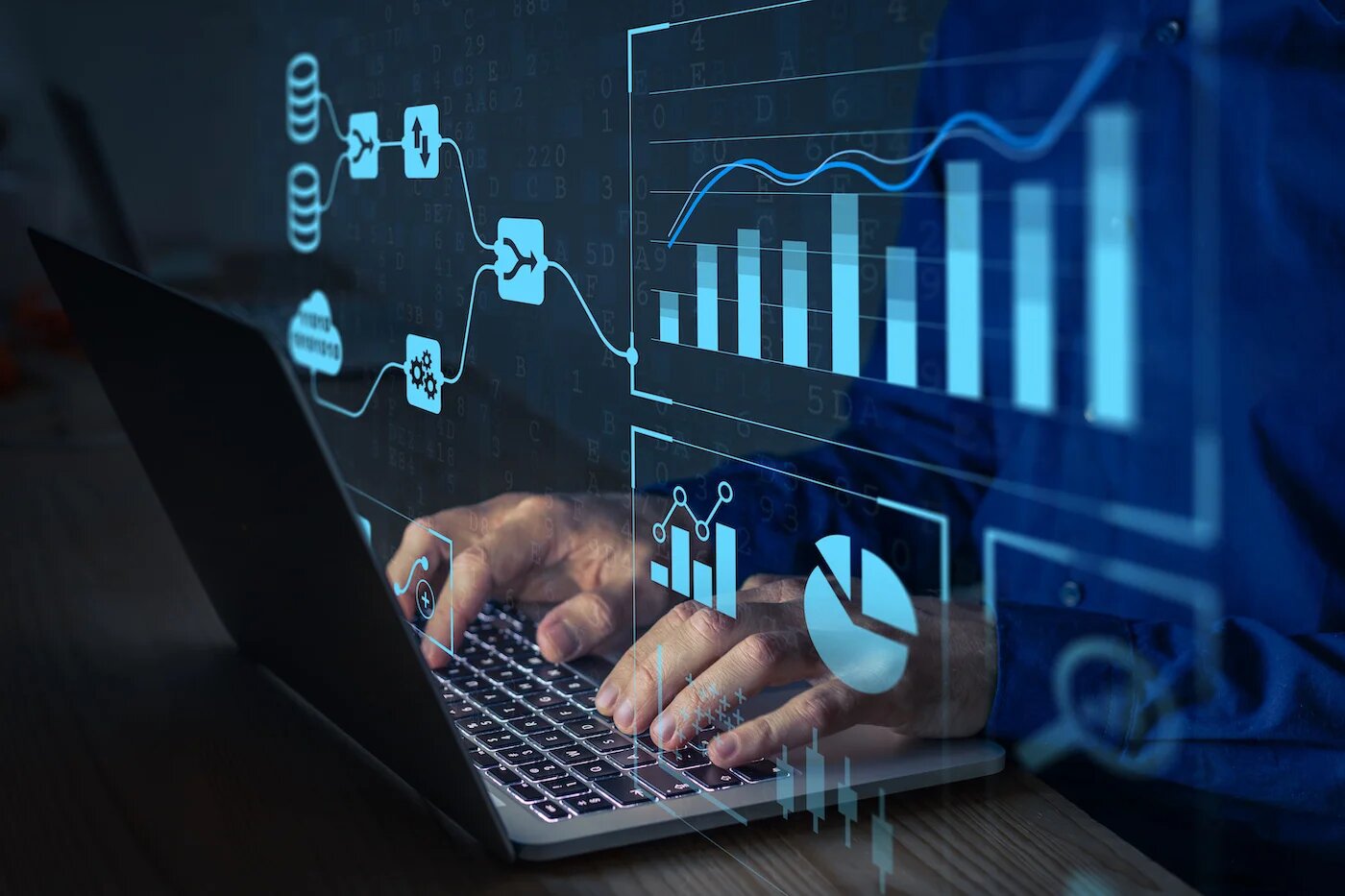
According to initial news reports, the shutdown occurred due to a malfunction in the system responsible for handling orders for incoming vehicle components. As The Guardian suggested, this malfunction could have disrupted Toyota’s “just-in-time” system.
Just in time is a logistics method to minimize costs by maintaining only the necessary parts for car assembly at specific assembly points. However, as evident, this approach crumbles when you cannot procure the required parts on time.
In their statement, Toyota expressed their apologies to “customers, suppliers, and related parties.”
The company regretted any inconvenience resulting from the suspension of its domestic plants.
“We would like to apologize once again to our customers, suppliers, and related parties for any inconvenience caused by the suspension of our domestic plants.”
~Toyota
Toyota’s Resolution and Preventive Measures
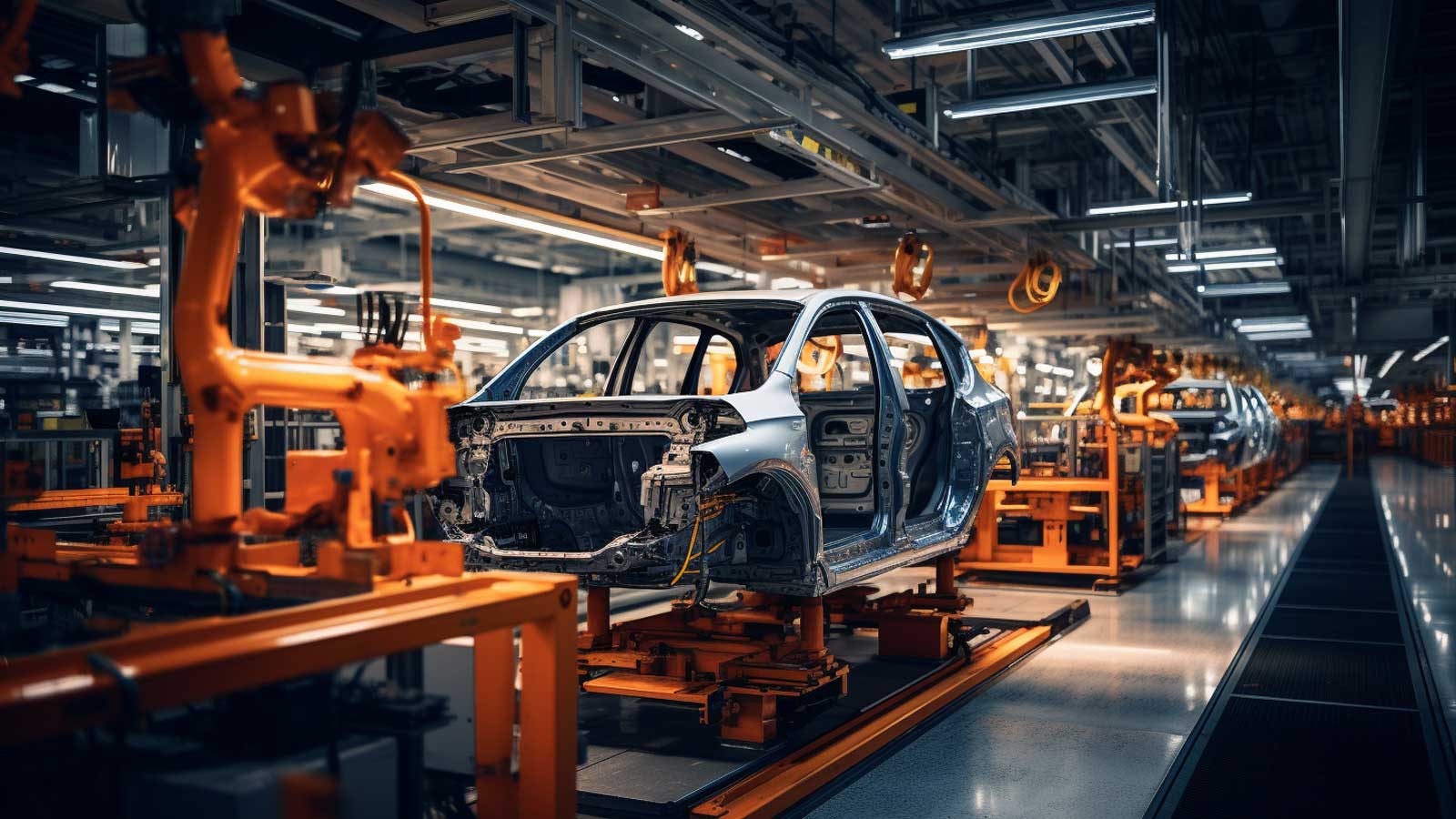
In response to the operational disruption, Toyota’s engineers successfully resolved the issue by migrating to a server with increased storage capacity.
This shift resulted in the resumption of plant operations the following day. The company has taken additional measures to prevent a recurrence by replicating and rigorously verifying the situation.
Amidst initial speculations of a potential cyberattack, Toyota clarified that security concerns were not the root cause of the disruption. The company emphasized its commitment to enhancing maintenance procedures in an unsigned communication. They aim to improve preventive efforts to ensure the uninterrupted production of vehicles, thereby meeting customer demands promptly.
Conclusion: Scalable, Flexible Data Storage Solutions are Critical!
The key takeaway from this narrative is evident. Partner with data storage providers that can ensure immediate access to additional storage capacity. This lesson is particularly relevant for large corporations relying on precise software timing to construct intricate machinery.
To cater to this pressing need, AiNET presents its robust cloud storage and computing solutions. Combining our data centers, fiber optic networks, and cloud storage, AiNET supports 1 billion people daily in keeping their systems up and running.
Join forces with AiNET today and experience unparalleled connectivity and resilience, all while reducing operational costs, finger-pointing, and vendor complexities